釉面砖干燥裂纹在生产中如何解决?
在釉面砖的生产过程中,无论是一次烧成还是二次烧成,坯釉裂纹是常见的质量缺陷之一。裂纹的种类多,产生原因复杂,解决方法也各异,生产技术人员对此并不陌生。笔者在生产实践中时常发现,看似简单的裂纹,有时并没有明显的辨别特征,一线生产技术人员分析时容易产生误判;甚至在查明裂纹的产生原因后,却因为生产条件的限制,导致问题迟迟不能完全解决,造成生产成品率的下降。
In the production process of glazed tiles, whether it is primary or secondary firing, glaze cracks are one of the most common quality defects. There are many types of cracks, complex causes, and various solutions, which are not unfamiliar to production technicians. The author often finds in production practice that seemingly simple cracks sometimes do not have obvious distinguishing features, and frontline production technicians are prone to misjudgment when analyzing them; Even after identifying the cause of the crack, the problem was delayed and could not be completely solved due to production conditions, resulting in a decrease in production yield.
根据裂纹的形成原因,釉面砖的常见裂纹大致可分为以下三种:一是机械碰撞裂纹,包括干压成型过程的脱模撞裂、翻坯机碰裂、橫线、平台及辊棒送砖过程造成的裂纹,等等。二是烧成冷却过程出现的裂纹。此类裂纹较长,或有弧形裂、锯齿裂等外观特征。三是干燥过程的裂纹,即干燥工艺参数控制不合理,干燥收缩导致的裂纹,包括边裂、中心裂、面裂等。特别是砖边缘部分的细裂纹,有时裂纹深度只比釉层深一点点,烧成前不易发现,常被忽视。这种裂纹与干燥曲线、坯料配方、粉料工艺参数都有关系。
According to the reasons for the formation of cracks, common cracks in glazed tiles can be roughly divided into the following three types: first, mechanical collision cracks, including demolding collision cracks during the dry pressing process, collision cracks caused by the turning machine, cracks caused by horizontal lines, platforms, and roller feeding processes, and so on. The second is the cracks that appear during the firing and cooling process. This type of crack is longer, or has appearance characteristics such as arc-shaped or serrated cracks. The third is the cracks during the drying process, which are caused by unreasonable control of drying process parameters and drying shrinkage, including edge cracks, center cracks, surface cracks, etc. Especially for the fine cracks on the edge of the brick, sometimes the crack depth is only slightly deeper than the glaze layer, which is difficult to detect before firing and is often overlooked. This type of crack is related to the drying curve, billet formula, and powder process parameters.
机械碰撞裂纹和冷却造成裂纹一般有明显的辨别特征,较易判断,而干燥导致的裂纹有时易与其它裂纹混淆,解决难度较大。笔者以两个工厂的实践解决情况为例,对干燥裂纹的解决方案进行探讨。
Mechanical collision cracks and cracks caused by cooling generally have obvious distinguishing features and are easy to determine, while cracks caused by drying are sometimes confused with other cracks and difficult to solve. The author takes the practical solutions of two factories as examples to explore solutions for drying cracks.
在釉面砖的生产中,单纯地讨论干燥裂纹的原因和解决方法并不算复杂,但在实际生产过程,因为和其它裂纹易于混淆,以致误判,或受制于设备、产量等客观条件,导致在工艺调整时瞻前顾后,常常达不到理想的效果。
In the production of glazed tiles, simply discussing the causes and solutions of dry cracks is not complicated. However, in the actual production process, it is easy to confuse with other cracks, leading to misjudgment or being subject to objective conditions such as equipment and output, which often leads to a lack of ideal results when adjusting the process.
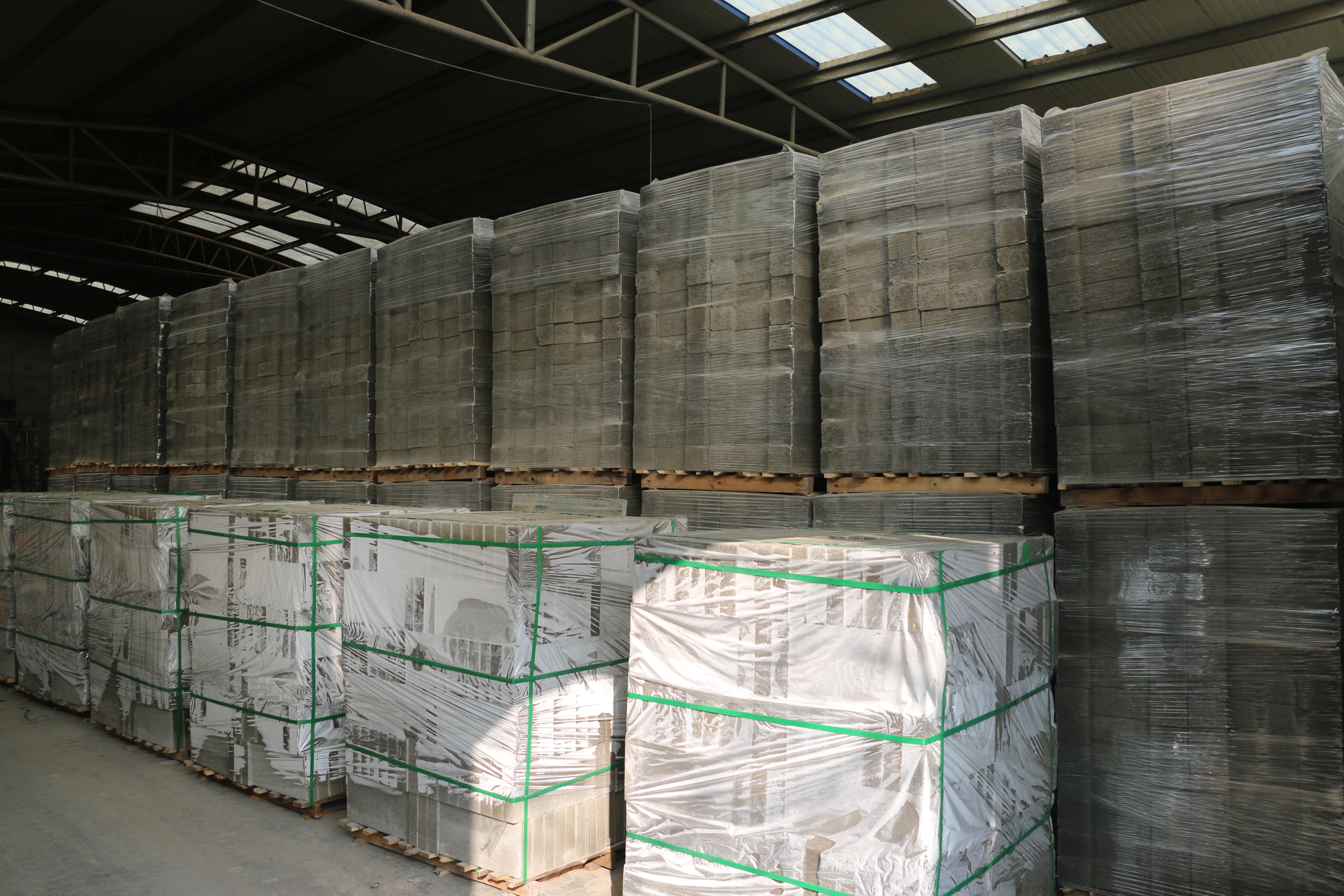
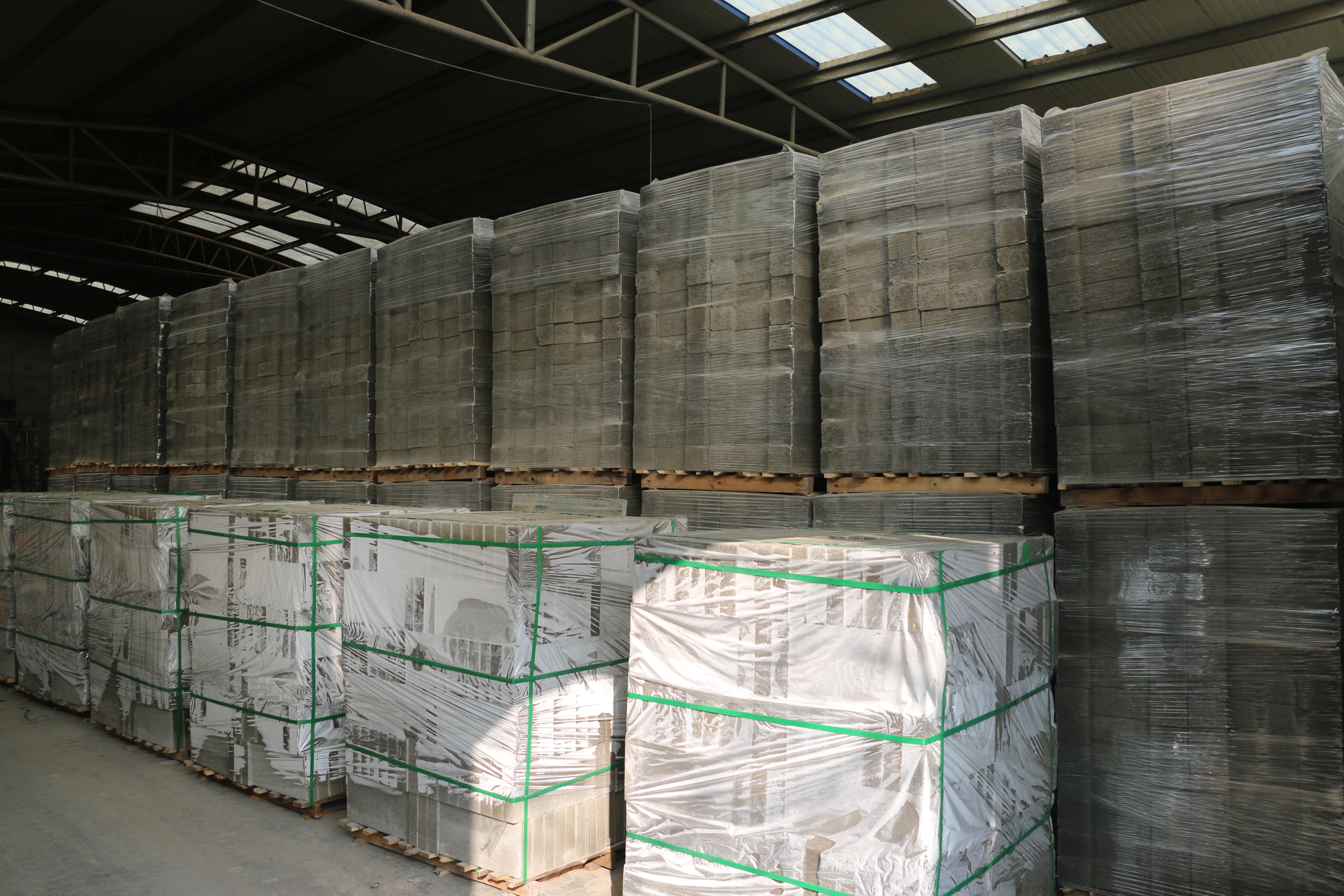
对裂纹不能只凭经验就下结论,要先采取措施进行细致排查,从压机模号、进砖顺序、窑内位置、烧成速度等方面,对裂纹的发生规律汇总分析。如果没有固定的位置规律,但烧成速度越快、规格越大、越厚的产品较常出现细边裂时,则要重点考虑是否干燥裂纹。在确定是干燥裂纹后,对粉料、烘干窑、坯料的工艺参数进行系统调整。一是提高粉料的粗颗粒比例,适当降低粉料的含水率,并增加成型压力,以保证足够的生坯强度。二是对烘干窑的干燥曲线进行调整优化,需注意保持烘干窑前段 “高温高湿”状态,整体可保持微正压气氛。三是调整坯料配方,适当引用少量强塑性原料或坯体增强剂,以减少干燥收缩大的塑性原料比例,提升生坯的干燥性能。后,对生产工艺参数加强检测分析,制定适合本厂的工艺标准,时常检查对照,才能保证长期稳定生产。
We cannot draw conclusions about cracks solely based on experience. We must first take measures to conduct a detailed investigation, summarizing and analyzing the occurrence patterns of cracks from aspects such as the press mold number, brick feeding sequence, kiln position, and firing speed. If there is no fixed position pattern, but the faster the firing speed, the larger the specification, and the thicker the product, the more frequent the occurrence of fine edge cracks, then the focus should be on whether to dry the cracks. After determining whether it is a dry crack, systematically adjust the process parameters of the powder, drying kiln, and billet. One is to increase the proportion of coarse particles in the powder, appropriately reduce the moisture content of the powder, and increase the molding pressure to ensure sufficient green strength. The second is to adjust and optimize the drying curve of the drying kiln, paying attention to maintaining the "high temperature and high humidity" state in the front section of the drying kiln, and overall maintaining a slightly positive pressure atmosphere. The third is to adjust the billet formula and appropriately use a small amount of strong plastic raw materials or billet reinforcement agents to reduce the proportion of plastic raw materials with large drying shrinkage and improve the drying performance of the green billet. Finally, strengthen testing and analysis of production process parameters, develop process standards suitable for our factory, and regularly check and compare them to ensure long-term stable production.
总之,对于干燥裂纹,只有多方面系统调整优化工艺,才能较彻底地解决问题,达到既快烧又节约能耗、充分发挥设备产能的理想目标。。
In short, for dry cracks, only by systematically adjusting and optimizing the process in multiple aspects can the problem be thoroughly solved, achieving the ideal goal of fast burning, energy saving, and fully utilizing equipment production capacity..
上一篇:电缆沟盖板的制作工艺介绍
下一篇:透水砖是否需要经常维护?
相关产品
相关新闻